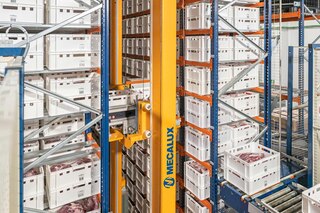
Kombinierter Zyklus von Regalbediengeräten: Kapazität oder Geschwindigkeit?
Unter kombiniertem Zyklus oder doppeltem Zyklus in einem automatisierten Lager versteht man die Bewegung, mit der ein Regalbediengerät eine Ware im Regal platziert und direkt anschließend innerhalb der gleichen Bewegung eine andere entnimmt.
Dabei ist daran zu denken, dass Regalbediengeräte wie Krane funktionieren, die sich innerhalb der Lagergänge bewegen und die Waren automatisch in den Positionen der Palettenregale absetzen und von dort entnehmen. Durch den kombinierten Zyklus werden die Bewegungen reduziert und somit die Abläufe beschleunigt.
Alle automatisierten Anlagen von Mecalux können kombinierte Zyklen ausführen, sofern der Betriebsablauf dies erfordert. Dadurch wird die Verwaltung der Ware erheblich beschleunigt. Dieses scheinbar einfache Konzept ist jedoch manchmal mit komplexen Berechnungen verbunden, die wir in diesem Artikel analysieren wollen. Beim Entwurf eines Lagers ist letztendlich zu entscheiden, ob mehr Wert auf eine höhere Zykluszahl oder auf eine größere Lagerkapazität gelegt wird.
Der Unterschied zwischen einfachem Zyklus und kombiniertem Zyklus
Beim einfachen Zyklus werden Ein- und Auslagerung der Waren in den Regalen unabhängig voneinander durchgeführt. Bei der Bewegung zur Einlagerung holt das Regalbediengerät die Ladeeinheiten lediglich am Regaleingang ab und platziert sie in den Regalen, um dann ohne Last wieder zum Regaleingang zurückzukehren. Bei der Entnahme wiederum holt das Regalbediengerät die Ware an ihrem Stellplatz ab und bringt sie zum Ausgang des automatischen Lagers. Der einfache Zyklus ist die normale Bewegung, wenn eine große Menge an Waren eingegangen ist und das Regalbediengerät diese lediglich einlagern muss, ohne etwas zu entnehmen. Er ist jedoch unpraktisch, wenn gleichzeitig Ein- und Auslagerungsbewegungen durchgeführt werden müssen.
Beim kombinierten Zyklus bewegt sich das Regalbediengerät mit der Last zunächst vom Regaleingang bis zur entsprechenden Lagerposition, an der es eine Palette oder einen Behälter absetzt. Anschließend bewegt es sich zu einem anderen Regalfach, wo es eine andere Last aufnimmt, die es dann zum Ausgangsförderer oder zu der Konsole am Ende des Gangs transportiert. Es ist offensichtlich, dass der Vorgang in diesem Fall viel effizienter ist, da in einer einzigen Bewegung zwei Aktionen durchgeführt werden, was die Leistung des Lagers erhöht.
Die Zykluszeit eines Regalbediengeräts
Die Zykluszeit ist der grundlegende Indikator, von der die Anzahl der Ladeeinheiten abhängt, die in einem automatisierten Lager in einem bestimmten Zeitraum bewegt werden können.
Die Zykluszeit lässt sich definieren als die Zeit, die ein Regalbediengerät benötigt, um eine Palette am Regaleingang aufzunehmen, sie im Regal abzusetzen, eine andere zu entnehmen und diese entweder zum gleichen Regaleingang oder dem am anderen Ende des Gangs gelegenen Eingang zu transportieren. Das heißt, sie setzt sich zusammen aus den konstanten Zeiten, die unabhängig von der Position der Ware sind, und den variablen Zeiten, die von den Bewegungen abhängen.
Die Zeiten hängen unmittelbar von den technischen Daten der Regalbediengeräte wie Beschleunigung, Geschwindigkeit, Positionierzeiten usw. sowie von den jeweils zurückzulegenden Strecken ab.
Anhand der verschiedenen Zykluszeiten lässt sich die mittlere Zykluszeit eines Regalbediengeräts abschätzen. Dies ist ein statistischer Wert, mit dem man eine ungefähre Vorstellung von der Kapazität der Bewegungen im Lager erhält.
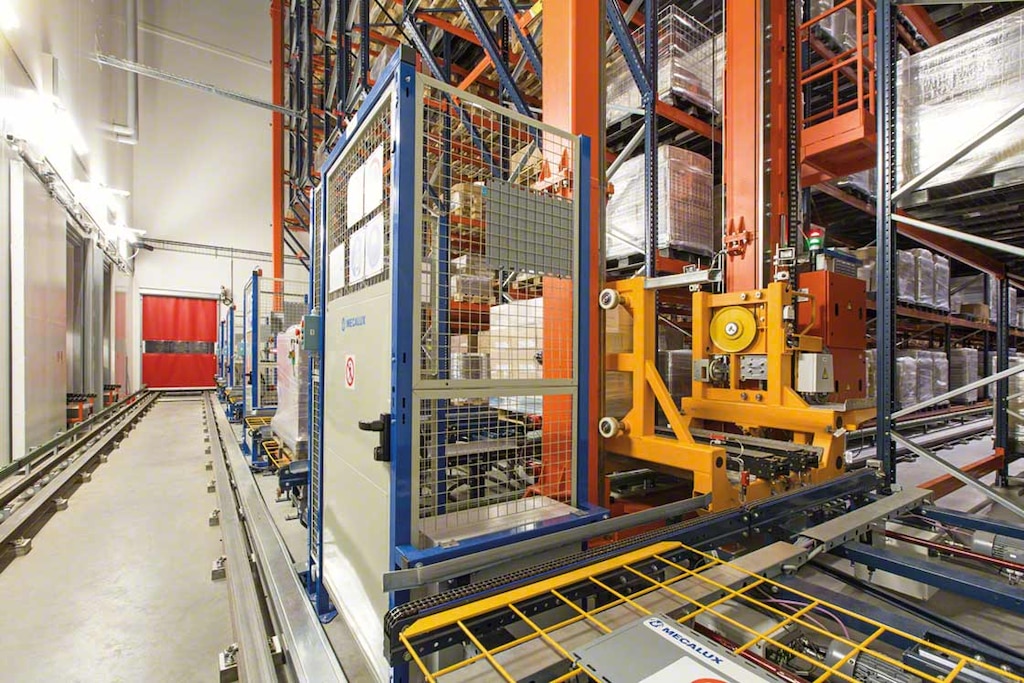
Berechnung der Anzahl der kombinierten Zyklen
Bei der Berechnung der Anzahl der kombinierten Zyklen, die ein Regalbediengerät bei Regalen mit einfacher Tiefe durchführen kann, ist unbedingt die Norm UNE 58912 zu berücksichtigen, die verschiedene Szenarien (Arten von möglichen Bewegungen) enthält, welche die Definition der Leistung eines automatischen Lagers ermöglichen. Die Berechnung gilt sowohl für automatische Paletten- als auch für Behälterlager.
Um die Zahlen für jedes einzelne Szenario zu berechnen, werden die Zeiten, die das Regalbediengerät benötigt, um sich von einem Punkt zu einem anderen zu bewegen, und die Transferzeiten für jede Bewegung addiert.
Es kann vorkommen, dass der Eingangspunkt (E) nicht mit dem Ausgangspunkt (A) übereinstimmt. Bei diesem Szenario muss auch die Zeit, die das Regalbediengerät vom Eingang bis zum Ausgang benötigt, addiert werden.

Das folgende Diagramm zeigt die ungefähre Anzahl der kombinierten Zyklen, die in Regalen mit einfacher Tiefe bei verschiedenen Regalhöhen und -längen erreicht werden können. Je länger das Regal ist, umso niedriger ist die Zykluszahl, da das Regalbediengerät dann längere Strecken zurücklegen muss. Analog dazu ist die Regalhöhe umgekehrt proportional zur Anzahl der kombinierten Zyklen pro Stunde (cc/h).
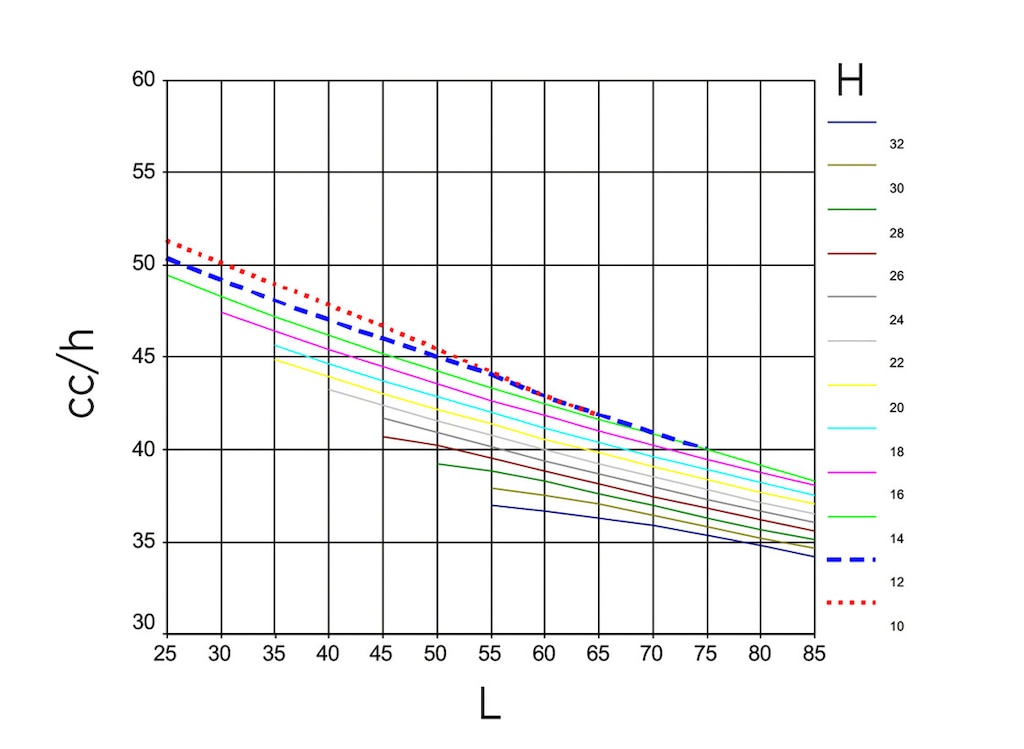
Kombinierte Zyklen in Regalen mit doppelter Tiefe
Was geschieht bei Regalen mit doppelter Tiefe? In diesen Fällen hängt die Zykluszeit des Regalbediengeräts nicht nur von der horizontalen Position und der Höhe der Stellplätze ab, sondern auch von der Regaltiefe. Bei der Berechnung der Zykluszahl kommt eine weitere Variable ins Spiel: der Belegungsgrad der Stellplätze.
Um auf die Ladeeinheit in der zweiten Position jedes Stellplatzes zuzugreifen, muss zunächst die erste Palette / der erste Behälter entnommen werden. Das Regalbediengerät muss dieses Produkt entnehmen und es an einem leeren Stellplatz absetzen. Die für diese Bewegung erforderliche Zeit wird als Gesamtzeit für die Fahrt zum nächstgelegenen leeren Stellplatz und die Rückkehr berechnet, einschließlich der Entnahme einer Palette / eines Behälters aus der Tiefe und der Lagerung in doppelter Tiefe. Die durchschnittliche Entfernung zum nächsten leeren Stellplatz hängt lediglich von der Belegungsrate des Lagers ab.
Bei der Berechnung der Lagerzyklen wird angenommen, dass die Hälfte der Zyklen mit einfacher Tiefe und die andere Hälfte mit doppelter Tiefe ausgeführt wird. Das folgende Diagramm zeigt Anzahl der kombinierten Zyklen in Regalen mit doppelter Tiefe in Abhängigkeit von der Höhe und Länge des Regals. Hier sehen wir, dass die Anzahl der Zyklen pro Stunde abnimmt, während die Lagerkapazität zunimmt. Das heißt, die Bewegungsgeschwindigkeit wird zwar verringert, aber der verfügbare Platz nimmt zu. Genau wie beim vorherigen Diagramm handelt es sich auch hier um eine Schätzung.
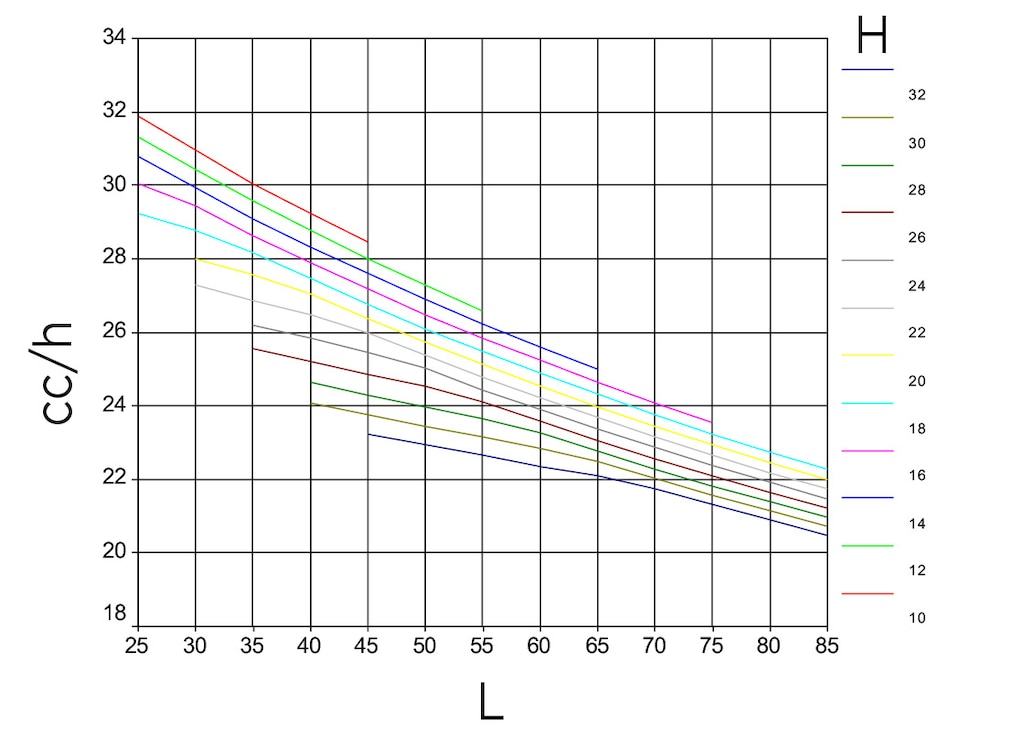
Gültigkeit der Berechnungen
Bei der Berechnung der Leistung eines Regalbediengeräts mithilfe der Norm UNE 58912 ist es notwendig, einen Parameter (a) zu ermitteln, der die Gültigkeit der durchgeführten Berechnungen validiert.
Der Parameter „a“ ist folgendermaßen definiert:
a = H/L × Vx/Vy
H = Höhe des Lagers
L = Länge des Lagers
Vx = Fahrgeschwindigkeit des Regalbediengeräts
Vy = Hubgeschwindigkeit des Regalbediengeräts
Beim „idealen“ Lager ist a = 1. Aufgrund dessen kann der Wertebereich von „a“ zwischen 0,5 und 2 liegen, um zuverlässige Ergebnisse im Rahmen der Norm UNE 58912 zu erhalten. Daher gilt:
0,5 ≤ a ≤ 2
Anpassung der kombinierten Zyklen an die jeweiligen Anforderungen
Kombinierte Zyklen führen zu einer deutlichen Verbesserung der Effizienz des automatischen Lagers. Es ist allerdings nötig, ein Gleichgewicht zu finden zwischen der Lagerkapazität (Höhe und Länge der Regale, einfache oder doppelte Tiefe) und der Anzahl der Zyklen pro Stunde, die durchschnittlich beibehalten werden sollen (Geschwindigkeit der Handhabung der Ware). Wenn es um die Automatisierung der Logistik geht, ist es entscheidend, die ideale Anzahl der kombinierten Zyklen zur effizienten Steuerung des Bewegungsflusses in einem Lager zu definieren.
Mecalux ist Spezialist dafür, dieses Gleichgewicht zwischen Lagerkapazität, Zykluszahl und Abmessungen des Lagers zu finden, um die logistischen Anforderungen eines jeden Unternehmens zu erfüllen. Wir bieten verschiedene Arten von Regalbediengeräten an und setzen digitale Simulationen (digitale Zwillinge) ein, die dazu dienen, die Funktionsweise des Lagers vor dessen Inbetriebnahme abzubilden und es so an die Anforderungen des Kunden anzupassen. Setzen Sie sich mit Mecalux in Verbindung, damit wir Ihnen bei der Suche nach der Logistiklösung, die Ihren Anforderungen am besten entspricht, helfen können.